Machine Guarding and Hand & Power Tools
Crushed hands and arms, severed fingers, blindness, etc. are part of a list of possible machinery related injuries. A good rule to remember is that any machine part, function or process which may cause injury must be safeguarded. When the operation of a machine or accidental contact with it can injure the operator or others in the vicinity, the hazards must be either controlled or eliminated.
Summary of Requirements
One or more methods of machine guarding shall be provided to protect the operator and other employees in the machine area from hazards such as those created by point of operation, nip points, rotating parts, flying chips and sparks. Examples of guarding methods are barrier guards, two-hand tripping devices, electronic safety devices, etc.
- Guards shall be affixed to the machine where possible and secured elsewhere if for any reason attachment to the machine is not possible. The guard shall be such that it does not offer an accident hazard in itself.
- Whenever engineering controls are not available or are not fully capable of protecting the employee, operators must wear personal protective equipment.
Training
Specific and detailed training is a crucial part of any effort to provide safeguarding against machine related hazards. Thorough operator training should involve instructions or hands-on training in the following:
- A description and identification of the hazards associated with particular machines;
- the safeguards themselves, how they provide protection, and the hazards for which they are intended;
- how to use the safeguards and why;
- how and under what circumstances safeguards can be removed, and by whom; and
- what to do if a safeguard is damaged, missing or unable to provide adequate protection.
This kind of safety training is necessary for new operators and maintenance or setup personnel, when any new or altered safeguards are put in service, or when workers are assigned to a new machine or operation.
Inspections
All safeguards provided meet the minimum OSHA requirements.
- The safeguards are firmly secured and not easily removable.
- The safeguards prevent workers hands, arms and other body parts from making contact with dangerous moving parts.
- Special guards, enclosures or personal protective equipment have been provided, where necessary to protect workers from exposure to harmful substances used in machine operations.
Safe Use of Hand Tool
- Hand tools must be used only for the purpose for which they are designed (e.g., a screwdriver must not be used as a chisel).
- Before each day’s use, employees must inspect hand tools for damage and defects.
- Wooden handles on hammers must not be loose, splintered, or cracked.
- Wrenches must not have loose or sprung jaws.
- Impact tools such as chisels, wedges, or drift pins must not have mushroomed heads.
- Cutting tools must not be dull. Dull tools can be more hazardous than sharp ones.
- Damaged or defective hand tools must be immediately tagged out (e.g., Unsafe — Do Not Use) and withdrawn from service for repair or replacement.
- Employees must not carry sharp tools in pockets unless the tools are sheathed.
- When using cutting tools, employees must cut in the direction away from their body.
Safe Use of Power Tools
- Portable cord-and-plug-connected power tools must be either grounded or double-insulated.
- Employees must shut off and disconnect tools when not in use, before servicing, and when changing accessories such as blades, bits and cutters.
- Guards and other safety devices must not be removed or defeated.
- Employees must inspect portable cord-and-plug-connected power tools and extension cords before each day’s use for:
- Loose parts.
- Deformed and missing pins.
- Damaged insulation.
- Evidence of possible internal damage (e.g., pinched or crushed insulation).
- Broken or cracked cases.
- Damaged or defective portable cord-and-plug-connected equipment must be immediately tagged out (e.g., Unsafe — Do Not Use) and withdrawn from service for repair or replacement.
DAMAGED OR DEFECTIVE POWER TOOLS ARE AN IMMINENT DANGER HAZARD AND MUST BE REMOVED FROM SERVICE IMMEDIATELY.
Repair of Cord-and-Plug-Connected Equipment
Repairs to cord-and-plug-connected equipment must be performed by a qualified person and must provide the same insulation and sheath qualities as originally manufactured. Tape repairs are not acceptable.
Use of Extension Cords
- TEMPORARY USE ONLY – not a substitute for permanent wiring
- Only heavy-duty “SO” rated extension cords with a ground conductor may be used. Flat appliance-type extension cords are unsafe for workplace applications and must not be used.
- Extension cords must be approved and suitable for conditions of use.
- Extension cords must not be used as substitute for the fixed wiring of a structure or be:
- Run through holes in walls, ceilings, or floors.
- Run through doorways, windows, or similar openings except for short-term work where the extension cord is not subject to damage.
- Attached to building surfaces or fastened with staples or otherwise hung in such a fashion that could damage the outer jacket or insulation.
- Concealed behind building walls, ceilings, or floors.
- Flexible cords and cables must be protected from accidental damage.
- Flexible cords must equipped with an attachment plug and must be energized from an approved receptacle outlet.
Continuity of Ground Conductor and Ground-Fault Circuit Interrupters (GFCIs)
- Employees must not use adapters (e.g., “cheater plugs”) that interrupt the continuity of the ground connection.
- Employees must connect power tools and similar equipment to a ground-fault circuit interrupter when working in wet or conductive environments.
Safe Use of Bench Grinders
- Employees must shut off and disconnect bench grinders when changing a wheel or adjusting the work rest.
- Guards and other safety devices must not be removed or defeated.
UNGUARDED BENCH GRINDERS ARE AN IMMINENT DANGER HAZARD AND MUST BE REMOVED FROM THE WORK AREA IMMEDIATELY.
3. Employees must inspect bench grinders before each day’s use. Employees should:
- Check the condition of the wheel
- Be sure that shields and guards are in place and properly adjusted.
- Ensure that the work rest is adjusted to within 1/8 inch of the wheel.
- Ensure (if present) an adjustable tongue guard is not greater that 1/4 inch
- Damaged or defective bench grinders must be immediately tagged out (e.g., Unsafe — Do Not Use) and withdrawn from service for repair.
- When using a bench grinder, employees must perform work from the wheel’s circumference.
Use of Compressed Air for Cleaning
- Employees must use approved nozzles that reduce air pressure to 30 psi or less.
- Employees must never use compressed air for personal cleaning.
Safe Use of Slings, Chains and Wire Ropes
- Employees must ensure that hoists, come-alongs, slings, chains and wire ropes are rated for the load to be lifted.
- Employees must inspect slings, chains and wire ropes for damage and defects before each use. Employees should check for:
- Corrosion.
- Excessive wear.
- A one-third reduction in outer wire diameter.
- Deformed links, hooks or eyelets.
- Distortion or kinking.
- Broken or frayed wires or the presence of exposed warning fibers.
- Damaged or defective slings, chains and wire ropes must be immediately tagged out (e.g., Unsafe — Do Not Use) and withdrawn from the work area for repair or disposal.
DAMAGED OR DEFECTIVE SLINGS, CHAINS AND WIRE ROPES ARE AN IMMINENT DANGER HAZARD AND MUST BE REMOVED FROM THE WORK AREA IMMEDIATELY.
Safe Practices for Lifting Loads with Slings, Chains and Wire Ropes
- The hoist operator must secure the load properly by:
- Using a sling(s), chain(s) or wire rope(s) of sufficient length so it will not be cut or deformed by the load.
- Slings must not be shortened with knots, bolts or other makeshift devices.
- Protecting the sling(s), chain(s) or wire rope(s) with padding when necessary to prevent cutting or abrasion.
- Securing the load so that it is sufficiently supported and will be stable.
- The hoist operator must lift the load safely by:
- Not placing their hands and fingers between the sling and its load while the sling is being tightened.
- Not allowing employees to ride loads.
- Lifting and moving the load slowly. Fast or jerky actions and shock loading must be avoided.
- Not standing directly below the load.
- Not moving the load over other people.
- Falling object hazard areas must be identified with signs, barricades or banner tape.
- The hoist operator must set the load down safely by:
- Being sure personnel are clear.
- Setting the load down slowly and maintaining control.
- Not pulling a sling, chain or wire rope out from under a load when the load is resting on the sling, chain or wire rope.
Safe Use of Powered Grounds Care Equipment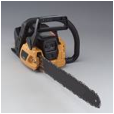
- Powered grounds care equipment (e.g., push mowers, edgers and trimmers) may only be operated by appropriately trained employees.
- Operators must inspect powered grounds care equipment before each day’s use for faulty or missing parts, especially guards and other safety devices.
- Operators must disengage all mechanical equipment, shut off the engine, and remove the wire from the spark plug (if not equipped with an ignition key) when powered grounds care equipment is being inspected, cleaned or serviced.
- Operators must never clear the discharge chute or otherwise place their hands near the blades or cutters of operating equipment.
- Damaged or defective power grounds care equipment must be immediately tagged out (e.g., Unsafe — Do Not Use) and withdrawn from service for repair.
MISSING OR DEFECTIVE SAFETY DEVICES EXPOSE GROUNDS CARE EQUIPMENT OPERATORS TO IMMINENT DANGER. DEFECTIVE EQUIPMENT MUST BE REMOVED FROM SERVICE IMMEDIATELY
- When refueling, operators must turn off the engine and wipe or allow any spilled fuel to evaporate before the engine is restarted.
- Powered grounds care equipment that is not in use or that is left unattended must be turned off
- Guards and other safety devices must not be removed or defeated.
- Operators must maintain powered grounds care equipment in a clean condition, free of excess oil and grease.
- Non combustible agents should be used for cleaning. Low flash point solvents must not be used.
- When starting powered grounds care equipment, operators must place the equipment on a secure surface and keep their hands and feet clear of moving blades and cutters.
- When operating powered grounds care equipment, operators must:
- Hold the equipment firmly with both hands placed on the equipment’s designated handholds.
- Ensure that their feet and hands are clear of moving blades and cutters, especially when the equipment is being pulled towards the operator.
- Be alert for the presence and location of other persons.
- Operators must instruct other persons to remain at a safe distance.
- Immediately shut off the equipment if a mechanical problem develops.
Contact Information
Kyle Mungavin, Assistant Director
Office: Service Building room 217
Phone: 257-3310